فهرست مطالب
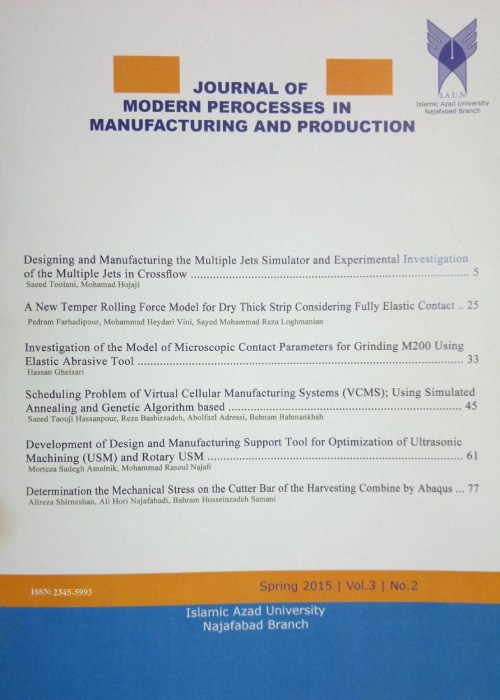
Journal of Modern Processes in Manufacturing and Production
Volume:12 Issue: 2, Spring 2023
- تاریخ انتشار: 1402/02/11
- تعداد عناوین: 6
-
-
Pages 5-21Blanking is a sheet metal cutting process, which itself is a prerequisite for many other forming processes. Punch and matrix shape and material, punch force and speed, lubricant, corner radius, and punch-matrix clearance are important variables in blanking. Clearance is critical in this process, depending on the material and sheet thickness, and is usually a percentage of the sheet thickness. Too much clearance causes the sheet to press and pull into the clearance area and Low clearance causes misaligned fracture lines and secondary cutting. Producing blanking with high thicknesses is always one of the challenges of the sheet metal blanking process. This study aims to create 57.5 mm diameter StW24 steel blanks with 12 mm thickness and a 38% penetration value. A blanking die was designed and built with different punches based on clearance values of 9, 15, and 21% to match the target drawing. Results show that increasing clearance from 9 to 15% leads to an 11% thicker rollover zone, 5% thicker fracture zone, and 33% thinner shear zone. Increasing clearance from 15 to 21% reduces the thickness of rollover, fracture, and shear zones by 24, 3, and 56% respectively. Increasing clearance from 9 to 21% also leads to a 51% increase in fracture angle and a 34% increase in burr size. Clearance of 15% of sheet thickness is best for producing blank as per the target drawing.Keywords: The sheet metal blanking, clearance, rollover zone, Shear zone, Fracture angle, burr, StW24
-
Pages 23-38Cryogenics is a field that involves producing, storing, transporting, and using materials at freezing temperatures. One application of this technology is in the shrinkage fitting process, where coolant materials like liquid nitrogen are used to reduce the dimensions of parts so that they can be joined together. This technique is often utilized in sub-assemblies to create a strong fit between the internal and external surfaces of components, which eliminates relative movement between parts, allowing force to be directly transferred from one part to another. In a recent study, we investigated different methods for fitting bush and axle parts with precise dimensions. Cryogenic, pressing, and thermal methods were utilized for assembly fitting. The cryogenic and thermal methods utilized contraction and expansion of parts for assembly fitting, while no dimensional changes occurred in press fitting. Results from the study showed that the cryogenic method required less force for the assembly and disassembly of parts, and the surface quality of the parts after disassembly was better compared to the other methods. Metallographic tests demonstrated that the microstructure of the parts did not change, and impact tests showed that there was no decrease in the toughness of the parts after the cryogenic operation. Based on these findings, the researchers concluded that the cryogenic method is an excellent technique for fitting SAE4140 Steel parts.Keywords: Cryogenics, Liquid nitrogen, Assemble, Disassemble, Fitting Process
-
Pages 39-52This paper describes the research, development, and optimization of a robotic welding system at a leading Irish AgriTech company. The project required the development of robotic welding fixtures using best design principles and the generation of associated weld programs to enable the automated welding of several products in the production system of the company. This study provides complete fixtures in line with customer requirements using Autodesk Inventor CAD software. By following an integrated methodology that links the industry standard approach to fixture design with product development tools including QFD, Pugh charts, and DFMEA, a defined structure to this process is provided, while ensuring transferability throughout the industry. It was found that the generation of an industry-ready robotic welding program using Panasonic DTPS software was aided by following a prescribed methodology. This complex process was streamlined by applying the defined coordinated approach enabling the gradual knowledge growth necessary to complete an industry-ready robotic program. The study demonstrates that moving from traditional manufacturing methods to robotization is possible for an SME. The benefits for enterprises seeking to replace mechanical manufacturing processes by adopting robotic welding systems and consequently capitalizing on the potential of this robotic technology are evident.Keywords: Robotic Welding, Fixture design, Industry 4.0, Internet of Things, Robotic Programming, AgriTech
-
Pages 53-79Circular manufacturing supply chains offer a novel and compelling perspective within the realm of supply chain sustainability. Consequently, the development of a suitable solution approach for circular manufacturing supply chains holds significant value. This study presents appropriate solution approaches for a mathematical model that has been formulated for a circular supply chain. To address the small-sized problem, the epsilon-constraint method is proposed. This method aids in obtaining a Pareto set of optimal solutions, facilitating the evaluation of trade-offs among three objectives. Given the NP-hard nature of the problem, the non-dominated sorting genetic algorithm (NSGA-II) is employed to approximate the Pareto front for larger problem sizes. A comparative analysis is conducted between the outcomes achieved in smaller dimensions using the epsilon-constraint method and those generated by the metaheuristic algorithm. The results indicate that the error percentage of the objective function, when compared to the epsilon method, remains consistently below 1%, underscoring the effectiveness of the proposed algorithm. These methodologies empower decision-makers to offer efficient, optimal solutions, enabling them to select the most suitable alternative based on budgetary considerations and organizational policies.Keywords: Circular Manufacturing Supply Chain, Optimization, epsilon-constraint, NSGA-II algorithm
-
Pages 81-88One of the main problems in sports medicine in today’s world is knee injuries. Champions of various sports fields often suffer from common knee injuries, such as injuries to the anterior cruciate ligament, middle cruciate ligament, medial collateral ligament of the knee, or meniscus. In this paper, a knee brace for general applications is modeled and its stress and strain analysis is calculated with the help of software. First, the displacement of the knee brace with ABAQUS software is investigated. By moving toward the top of the knee brace, the amount of displacement decreases. So that at least the amount of displacement is in the upper part of the knee brace. In the next part, the amount of strain and strain for this knee brace is investigated. The amount of stress in the upper part of the knee brace is higher than in other places. Additionally, the amount of strain for this knee brace is determined, the knee brace in the upper part, on the inner side of the knee brace, bears more strain. The results show that this knee brace can be easily produced and considered for different applications.Keywords: CAD Model, Finite Element, Knee Brace, Simulation
-
Pages 89-102This study evaluated the effects of peening angle and time on the microstructure and wear behavior of AZ31 alloy subjected to the shot peening process. The samples were shot peened at 30° and 45° for 20 and 80 min with steel pellets. The microstructures and grain sizes of the shot peened samples were studied by scanning electron microscopy (SEM) and X-ray diffraction (XRD). In addition, the samples were characterized through hardness and wear measurements. The results showed that shot peening time had a greater effect on grain refining than shot peening angle. In addition, the hardness was increased to 206% for the sample shot peened at 45° for 80 min. This can be ascribed to reduced grain sizes on the surface (crystallite size of 169 Å) and increased micro-strains. The wear test revealed that the wear resistance of the sample was increased with increasing the peening angle and time. Furthermore, the mechanisms of adhesive and abrasive wear were observed for untreated and shot-peened specimens.Keywords: Shot Peening, AZ31 Alloy, Peening Angle, Peening Time, Wear